Article Navigation
- Overview & Composition
- Key Performance Advantages
- Industrial Applications
- Procurement Strategies
- Why Choose Kerui?
1. Overview & Composition
Magnesia spinel bricks are high-performance refractory materials composed of magnesia (MgO) and spinel (MgAl₂O₄), renowned for their exceptional thermal shock resistance and corrosion stability in aggressive alkaline environments. Kerui Refractory’s magnesia spinel bricks are engineered to deliver:
- Superior Thermal Stability: Operate continuously at 1,700–1,800°C.
- Slag Resistance: Neutralize acidic slags (SiO₂, FeO) in steelmaking and cement kilns.
- Hydration Resistance: Stabilized microstructure prevents MgO hydration in humid conditions.
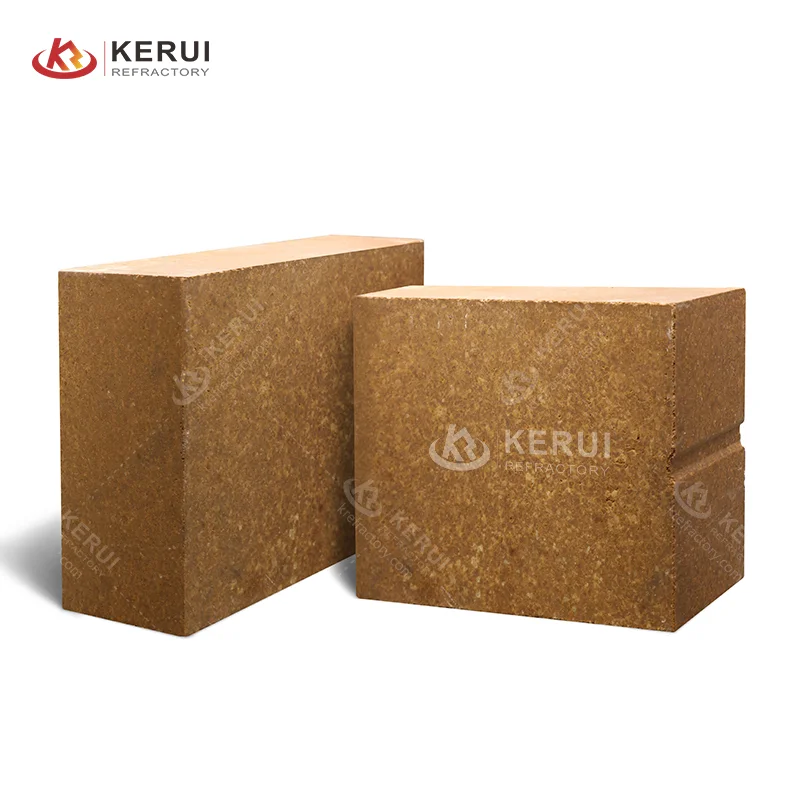
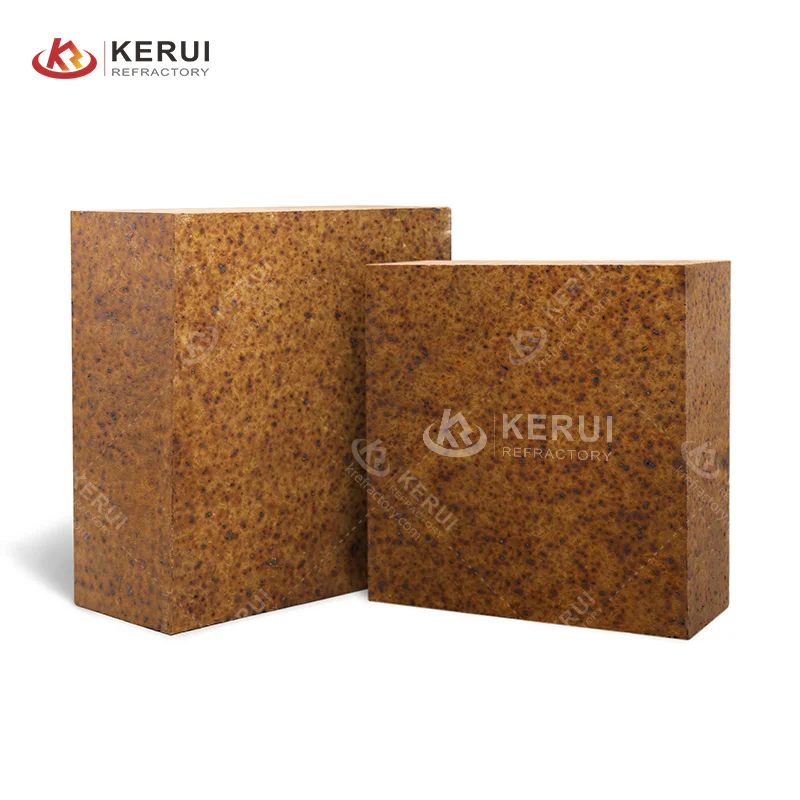
2. Key Performance Advantages
2.1 Technical Specifications
Parameter | Kerui MS-85 | Industry Standard | Test Method |
---|---|---|---|
MgO Content | 75–85% | 70–80% | XRF Analysis |
Al₂O₃ Content | 8–15% | 5–12% | XRF Analysis |
Apparent Porosity | 12–16% | 15–20% | ASTM C20 |
Cold Crushing Strength | 80–150 MPa | 50–100 MPa | ASTM C133 |
Thermal Shock Resistance | >30 cycles (1,100°C ΔT) | 15–25 cycles | ASTM C1171 |
Refractoriness Under Load | 1,700°C | 1,600–1,650°C | ASTM C113 |
2.2 Comparative Benefits
- Thermal Expansion: 30% lower than magnesia-chrome bricks, reducing crack formation.
- Corrosion Resistance: 2x longer lifespan vs. dolomite bricks in cement kiln transition zones.
3. Industrial Applications
3.1 Steel Industry
- Ladle Linings: Resist slag penetration (CaO-SiO₂-Al₂O₃) during secondary refining.
- RH Degassers: Handle vacuum cycling and molten steel splashing.
3.2 Cement Production
- Rotary Kiln Transition Zones: Combat alkali sulfate and chloride attacks.
- Preheater Cyclones: Withstand high-velocity abrasive raw meal particles.
3.3 Non-Ferrous Metallurgy
- Copper Smelting Furnaces: Stable in sulfur-rich and oxidizing atmospheres.
- Aluminum Holding Furnaces: Resist molten aluminum penetration.
4. Procurement Strategies
4.1 Cost & MOQ Overview
Brick Grade | Price Range (FOB) | Min Order Quantity | Bulk Discounts (>15 tons) |
---|---|---|---|
Standard (MgO 75–80%) | $1,200–2,000/ton | 5 tons | 5–10% |
Premium (MgO 80–85%) | $2,500–3,800/ton | 3 tons | 8–12% |
Custom Formulations | $3,000–5,000/ton | 1 ton | 10–15% |
4.2 Supplier Selection Checklist
- ✅ Certifications: ISO 9001, ASTM C455 compliance.
- ✅ Spinel Content: Verify spinel phase ≥20% via XRD analysis.
- ✅ Customization: Availability of arc, wedge, and skew shapes.
4.3 Installation & Maintenance
- Mortar Compatibility: Use magnesia-spinel mortar for ≤2mm joints.
- Preheating Protocol: Ramp temperature at ≤50°C/hour to 600°C.
5. Why Choose Kerui?
5.1 Advanced Manufacturing
- Reactive Spinel Technology: Kerui’s Magnesia spinel bricks feature pre-synthesized spinel grains for 40% higher corrosion resistance.
- Eco-Friendly Production: Chromium-free formulations comply with EU REACH regulations.
5.2 Global Service Excellence
- Fast Turnaround: 80% of orders ship within 15 days, even for custom geometries.
- Technical Support: Free kiln lining audits and failure mode analysis.
5.3 Success Story
A European cement plant using Kerui’s Magnesia spinel bricks in a 5,000 TPD kiln transition zone reported:
- 50% reduction in annual downtime for relining.
- Lining lifespan extended from 12 to 24 months.
Conclusion
Magnesia spinel bricks are indispensable for industries requiring extreme thermal and chemical stability. Kerui Refractory—a leader in advanced ceramic solutions—delivers high-performance magnesia spinel bricks backed by 12+ years of R&D expertise, ensuring unmatched durability and cost efficiency.
Act Now:
- 📩 Request a custom quote for tailored solutions.
- 📞 Contact +86 153 7871 8880 for samples or technical support.
Performance data based on ASTM standards and Kerui’s internal testing. Results may vary by operational conditions.